
08106652505
SATISFACTION GUARANTEED
Quality and Excellence is
what defines us!
____________
Quality assurance, reliability and accountability are the primary core values that distinguish us in the superior class of the HSE sector
ENVIRONMENTAL PROTECTION MATERIALS: Oil Booms / Spill Response
To help maintain a cleaner, safer workplace environment, We distribute a complete line of high-tech sorbents for almost every leak and spill application. We have in stock over 350 SpillTech® Sorbents to choose from including mats, pads, rolls, socks, pillows, pans, drum top pads, booms and spill kits.
REPRESENTING LEADING MANUFACTURERS IN FIRE PROTECTION & SECURITY
Kensteve Oilfield & Allied Services Nigeria Ltd (KOASNL), an Internationally Certified distribution organization part of a larger group is a specialist distributor of a wide range of fire extinguishers, other fire protection products.
DISTRIBUTOR OF FIRE FIGHTING MATERIALS & EQUIPMENT
KSOASNL was established to provide a new level of services in the Distribution and Maintenance of Firefighting, Protection & Oil Spill Equipments. Our Future is guaranteed by our extensive experience and solid performance with our clients in the past.
KOASNL's Vision Is To Be Among The leading Indigenous Companies In The Protection Of Life,
Property And Environment.
Our Mission Is To Pioneer The Delivery of Innovative Technology And Services That Continually Protect And Support/Restore lives, Properties And Environment.

WELCOME
SATISFACTION GUARANTEED
Quality and Excellence is what defines us!
Quality assurance, reliability and accountability are the primary core values that distinguish us in the superior class of the HSE sector
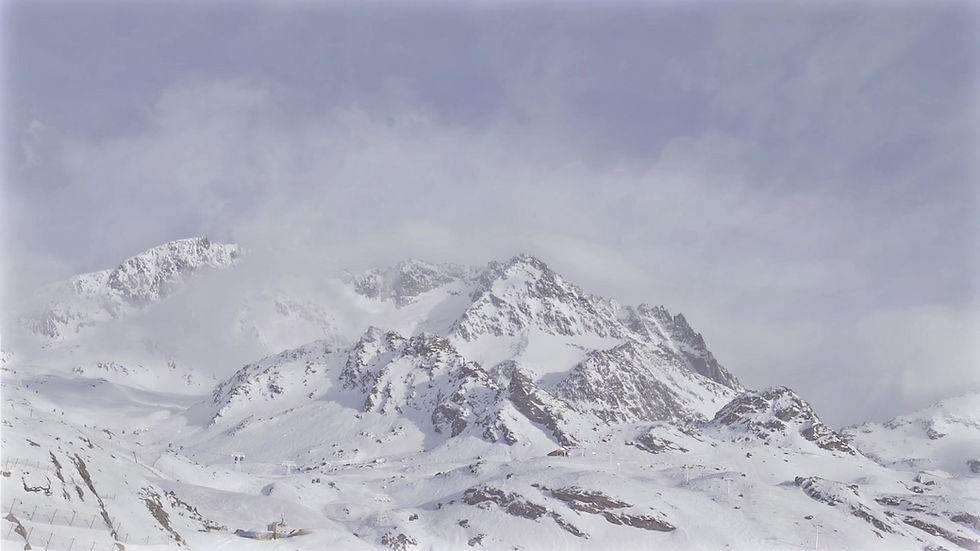
Top Fire Protection Equipment Supplier, maintenance and services, of oil spill recovery materials In Nigeria
KENSTEVE OILFIELD & ALLIED SERVICES NIG. LTD is an indigenous Nigerian company owned by Engr. Kenechukwu Lawrence MSc in electrical and electronics Engineering, the company was incorporated in 2012 to provide a broad spectrum of services and expertise to the Engineering sectors.
This broad capability enables us to satisfy our clients with a full range of Major stocklist of fire safety & Environmental protection materials & equipment.
KENSTEVE OILFIELD & ALLIED SERVICES NIG. LTD was established to provide a needed level of services in the Distribution and Maintenance of Fire Fighting Materials and Equipment. Our Future is guaranteed by our extensive experience and solid performance with our clients in the past.
KENSTEVE OILFIELD & ALLIED SERVICES NIG. LTD has deployed progressive methods to ensure that innovation and quality are prioritized for the benefit of clients. The company’s business is built on the strategy of having vertically integrated operations, which improve efficiency and timeliness of project execution.
The company is dedicated to serving its strong and diverse customer base which will include most of the major multinational exploration and production companies, many of the large and midsized local independents, and a number of the smaller producers.
We have trained and experienced personnel in our team who have been involved in marine and related services that can provide your organization with the best services you desire.
Our Philosophy
KENSTEVE OILFIELD & ALLIED SERVICES NIG. LTD.'s corporate philosophy is to engage in ethical business with a focus on the use of the latest technology, building safety culture and environment protection with commitment towards fruitful engagement and maximum return for local and host communities.
KENSTEVE OILFIELD & ALLIED SERVICES NIG. LTD Promotes a time tasted work culture of honesty, integrity, punctuality, discipline, and selfless dedication in transacting its business. It firmly believes in human capability and has always invested in the theory of the “right person for the right job”. Since its founding, 11 years ago KSOASNL has continued to foresee the need to provide total fire and oil spillage protection capabilities.
KSOASNL is also supported by a team of qualified engineers and professionals within and outside the country, In other ways, KSOASNL is in a position to provide Fire and Safety Protection Engineering as well as oil and gas spillage/diffusion control services in a most cost effective way.
KSOASNL’s reputation for quality and reliability has made it a trusted name all over the country. Our position as marketers was built on total dedication and pride in job well done and foreseeing the needs of the industries, Government establishment in individual and cooperate requirements.
KSOASNL has helped countless individuals and companies to effectively prevent dangerous and costly fires, oil spillage,, and gas explosions. This includes households, offices, high-rise buildings complexes, factories, aircraft hangers, Power generation plants, Ports, Stadiums and other huge installations.
KSOAS’S MAJOR PRODUCT LINE AND SERVICES ARE:
1. All types and sizes of fire extinguishers (portable & mobile, low pressure & high pressure)
2. Dry Powder, CO2, Foam, Water, FM 200, FE 36, and wet chemical.
3. Fire fighting Hoses, Nozzles, Ramps Fire hose reels and cabinets.
4. Fire hydrant (all types & sizes) Booster Pump sets dry & Wet riser equipment's.
5. All types of valves, sprinkler systems, fire Alarm System, (Analogue, Addressable & Conventional) Emergency Lighting System.
6. Fire Detection Systems, Foam System & equipment's.
7. FM 200 Fire Suppression System, C02 Extinguishing System and Gas Automatic Extinguishing system.
8. Fire Blanket & Safety Equipment, Fire Vehicles, Trucks, trailers Rescue Vans,
Breathing Apparatus, Fire Proximity & entry Suits.
9. Oxygen Filling machines.
10. All types of Filling Machines for C02, Dry Power and Clean Agent.
11. Combustible and poisonous gasses detection systems and units.
12. Oil Spillage Control consumables, Equipment's and machineries.
13. Personal Protective, Clothing/Wears, Oil spill control chemicals environmental cleaning chemical/degreasers, for Example cold wash.
14. OIL SPILL RESPONSE MATERIALS INCLUDE Oil Spill Kit, 50 Gallon Capacity Oil Absorbent Booms,
15. Oil Absorbent Rolls Oil Absorbent PadsOil Absorbent Pillows Oil Absorbent Particulates
16. Polypropylene Type Biodegradable, Particulates Oil Petroleum Spill Dispersant Chemical Suite, Chemical Handling Hand gloves
17. Chemical Spill Kits,
18. All Types And Sizes Of Chemical Absorbent Containment Boom, Ropes, And Anchor Collapsible/ Fast Floating Tanks For Crude Oil Spill Recovery And StoragePop Up Pools Spate Pump And Skimmers E.T.C
Fire Extinguishers
our range of extinguishers
Fire and Safety Solutions are able to offer a full range of fire extinguishers, suitable for both domestic and commercial use. In addition to this, our extinguishers also come in a range of finishes, from traditional to premium (which has a higher quality finish and is a slightly higher specification, through to chrome finished extinguishers. Below is a selection of our range, for full details please contact us.
Water Extinguisher
Signal Red
Best For
Fires involving organic solid materials such as wood, cloth, paper, plastics, Coal etc.
Danger
Do not use on burning fat or oil or on electrical appliances
How to Use
Point the jet at the base of the flames and keep it moving across the area of the fire. Ensure that all areas of the fire are out.
How it Works
Water has a great effect on cooling the fuel surfaces and thereby reducing the pyrolysis rate of the fuel
Water Spray Extinguisher (Water with additive)
Signal Red
Best For
Fires involving organic solid materials such as wood, cloth, paper, plastics, Coal etc. These offer significantly improved fire fighting capability than traditional jet type water fire extinguishers. Available in 3 and 6 litres.
Danger
Do not use on burning fat or oil or on electrical appliances
How to Use
Point the jet at the base of the flames and keep it moving across the area of the fire. Ensure that all areas of the fire are out.
How it Works
Water has a great effect on cooling the fuel surfaces and thereby reducing the pyrolysis rate of the fuel. Instead of a jet nozzel a spray nozzel is used, with a higher pressure, which creates a fine spray. This allows for a given quantity of water to have a considerable increase in the surface area presented to the fire. This makes extinguishing more efficient by more rapid extraction of heat, formation of steam etc. They can also contain surfactants which help the water penetrate deep into the burning material which increase the effectiveness of the extinguisher.
Water Mist Extinguisher (‘Dry’ Water Mist)
Signal Red on a White Background
Best For
The first broad spectrum extinguisher to tackle A, B, C rated risks as well as fats, deep fat fryers (Class F). Models with dielectric test to 35k Volt can be safely used on electrical fires (up to 1000 Volt) if a safety distance of 1m is adhered to, as their mist (de-ionised water) does not conduct electricity and the extinguisher does not normally form puddles, which could conduct electricity.
Danger
N/A
How to Use
Point the jet at the base of the flames and keep it moving across the area of the fire. Ensure that all areas of the fire are out.The fire draws the microscopic water particles into the fire
How it Works
Water is turned into microscopic particles in the supersonic nozzle. The water mist is drawn to the fire where it cools and suffocates the fire. The mist also forms a safety barrier between user and fire, which keeps some of the heat back.
Powder Extinguisher (Multi-Purpose)
Blue
Best For
Can be used on fires involving organic solids, liquids such as grease, fats, oil, paint, petrol, etc but not on chip or fat pan fires. Can also be used on gas fires.
Danger
Safe on live electrical equipment, although does not penetrate the spaces in equipment easily and the fire may re-ignite. This type of extinguisher does not cool the fire very well and care should be taken that the fire does not flare up again.
Smouldering material in deep seated fires such as upholstery or bedding can cause the fire to start up again. Do not use on domestic chip or fat pan fires.There is danger of inhalation if powder extinguishers are used within buildings.
How to Use
Point the jet or discharge horn at the base of the flames and, with a rapid sweeping motion, drive the fire towards the far edge until all the flames are out. If the extinguisher has a hand control, wait until the air clears and if you can still see the flames, attack the fire again.
How it Works
Similarly to almost all extinguishing agents the powders acts as a thermal ballast making the flames too cool for the chemical reactions to continue. Some powders also provide a minor chemical inhibition, although this effect is relatively weak. These powders thus provide rapid knockdown of flame fronts, but may not keep the fire suppressed.
Dry Powder Extinguisher (Special Powders)
Blue
Best For
These specialist powder extinguishers are designed to tackle fires involving combustible metals such as lithium, magnesium, sodium or aluminium when in the form of swarf or powder.
There are three special powders based on graphite, copper and sodium chloride.
Danger
Do not allow water to come in contact with the burning metal and the powder must be gently applied. Sodium Chloride is not recommended for Lithium.
How to Use
The lance enables the user to tackle fire at a safe distance and the low velocity applicator to reduce the energy of the jet allowing the powder to gently smother the surface of the burning material thus avoiding scattering of high temperature particles and stimulating the formation of a crust. The method of application is completely different from a standard extinguisher and user training is required. They are not suitable for use on live electrical fires.
How it Works
This extinguisher works by forming a crust which insulates the metal to prevent access to other combustible material nearby and smothering the fire to prevent oxygen from the atmosphere reacting with the metal
Foam Extinguisher (AFFF)
Cream
Best For
Fires involving solids and burning liquids, such as paint and petrol but not suitable for chip or fat pan fires. Safe on fires caused by electricity if tested to 35kV (dielectric test) and a 1m safety distance is adhered to.
Danger
Do not use on chip or fat pan fires.
How to Use
For fires involving solids, point the jet at the base of the flames and keep it moving across the area of the fire. Ensure that all areas of the fire are out. For fires involving liquids, do not aim the jet straight into the liquid. Where the liquid on fire is in a container, point the jet at the inside edge of the container or on a nearby surface above the burning liquid. Allow the foam to build up and flow across the liquid.
How it Works
They are mainly water based, with a foaming agent so that the foam can float on top of the burning liquid and break the interaction between the flames and the fuel surface.
Carbon Dioxide Extinguisher
Black
Best For
Live electrical equipment, although it allows re-ignition of hot plastics. Now mainly used on large computer servers, although care has to be taken not to asphyxiate people when using the extinguisher in small server rooms.
Danger
Do not use on chip or fat pan fires, as it carries burning fat out of container. This type of extinguisher does not cool the fire very well and you need to ensure that the fire does not start up again. Fumes from CO2 extinguishers can asphyxiate if used in confined spaces: ventilate the area as soon as the fire has been controlled.Only use CO2 extinguishers with frost-free horns, as the hand holding the horn can otherwise be frozen to the horn, as the gas is getting very cold during the discharge.
How to Use
The discharge horn should be directed at the base of the flames and the jet kept moving across the area of the fire.
How it Works
Carbon dioxide extinguisher works by suffocating the fire. Carbon dioxide displaces oxygen in the air. However, once discharged, the CO2 will dissipate quickly and allow access for oxygen again, which can re-ignite the fire.
Wet Chemical
Canary Yellow
Best For
Wet chemical fire extinguishers are ideal for Class F fires, involving cooking oils and fats, such as lard, olive oil, sunflower oil, maize oil and butter.
Danger
Check manufacturer’s instructions for suitability of use. These extinguishers are usually not recommended for class B fires such as petrol, although Gloria has produced a 3l wet chemical extinguisher with B rating.
How to Use
Apply the wet chemical using the extended applicator in slow circular movements, which give a gentle, yet highly effective application. Apply the fine spray onto the burning fat until the surface of the burning cooking oil changes into a soapy like substance which prevents re-ignition. The gentle application helps to prevent burning oil splashing out of the container. Make sure that you empty the entire content of the wet chemical extinguisher onto the oil/fat, as the fire can re-ignite otherwise.
How it Works
Most class F extinguishers contain a solution of potassium acetate, sometimes with some potassium citrate or potassium bicarbonate. The extinguishers spray the agent out as a fine mist. The mist acts to cool the flame front, while the potassium salts saponify the surface of the burning cooking oil, producing a layer of foam over the surface. This solution thus provides a similar blanketing effect to a foam extinguisher, but with a greater cooling effect. The saponification only works on animal fats and vegetable oils, so most class F extinguishers cannot be used for class B fires. The misting also helps to prevent splashing the blazing oil.
Tests have established that a 6 litre wet chemical fire extinguisher with a 75F rating can deal with a fat fire of maximum 0.11 m2 surface area.
Fire Blanket
Fire Blanket Fire blankets are made of fire resistant materials. They are particularly useful for smothering flammable liquid fires or for wrapping round a person whose clothing is on fire. Fire blankets conforming to British Standard BS EN 1869 : 1997 are suitable for use in the home BS 7944 : 1999 is suitable for industrial use. These will be marked to show whether they should be thrown away after use or used again after cleaning in accordance with the manufacturers instructions.
Best For
Fires involving both solids and liquids. Particularly good for small clothing fires and for chip and fat pan fires providing the blanket completely covers the fire.
Danger
If the blanket does not completely cover the fire, it will not be able to extinguish the fire.
How to Use
Place carefully over the fire. Keep your hands shielded from the fire. Do not waft the fire towards you.
How it Works
Smothers the fire and prevents oxygen getting to the fire.
Hose Reel
Best For
Fires involving organic solid materials such as wood, cloth, paper, plastics, coal etc.
Danger
Do not use on burning fat or oil or on electrical appliances before the electric supply has been isolated.
How to Use
Point the jet at the base of the flames and keep it moving across the area of the fire. Ensure that all areas of the fire are out.
How it Works
Water has a great effect on cooling the fuel surfaces and thereby reducing the pyrolysis rate of the fuel.
Fire Buckets
A simple bucket of water can be used on Class A type of fires either to supplement a water extinguisher or as a first attack if an extinguisher is not immediately available. It also can be filled with dry sand and used as an absorbing agent or to dam a flow of flammable liquid. They do have serious disadvantages as they are often misused, left empty or allowed to be used as a refuse container.
Best For
Wood, Cloth, Paper, Plastics, Coal
Danger
Do not use on burning fat or oil or on electrical appliances before the electric supply has been isolated.
How to Use
Throw at the base of the flames. Ensure that all areas of the fire are out.
How it Works
Water has a great effect on cooling the fuel surfaces and thereby reducing the pyrolysis rate of the fuel
Contempo Fire Extinguishers
Contempo Fire Extinguishers
a range of fire extinguishers with an elegant finish
What are Contempo Fire Extinguishers?
We’re all used to the traditional finish of a fire extinguisher, but there are some circumstances where a high quality, hand finished superior extinguisher that is both effective in fighting fire yet a pleasing design is required. Fire and Safety Solutions Ltd are pleased to be able to provide just such a range of fire extinguishers – the Contempo range, blending practicality with beautiful design.
Whether you are looking for a an Antique Copper finish fire extinguisher to blend in to a heritage house or period building, or an ultra modern polished stainless steel extinguisher for a contemporary office or home, the Contempo range can provide this.
Sizes Available (depending on extinguisher type):
-
6ltr
-
9ltr
-
2kg
-
5kg
-
6kg
Finishes Available:
-
Polished Gold
-
Polished Stainless Steel and Chrome
-
Brushed Antique Copper
Key Features:
-
Full range of spare parts available
-
Corrosion-resistant finish
-
5-year warranty
-
Plastic base skirt for protection
-
Polyethylene internal lining (on Water and Foam units)
5 Year Guarantee
We are 100% confident in our products and services which is why our fire extinguishers come with a 5 year guarantee as standard for your complete peace of mind.
Polished Gold Fire Extinguishers
The is the ultimate in luxury extinguishers, polished gold extinguishers don’t just blend into their surroundings – they look part of it. Each extinguisher is electro plated to give a stunning mirror finish. Available with matching polished gold tubular stands and ID signs and in the following sizes and extinguisher types:
-
6ltr Water Polished Gold Extinguisher
-
6ltr Foam Polished Gold Extinguisher
-
6ltr MultiChem Polished Gold Extinguisher
-
CO2 Polished Gold Extinguisher
-
6kg Powder Polished Gold Extinguisher
Polished Stainless Steel and Chrome Fire Extinguishers
With it’s modern, highly polished finish, Steel and Polished extinguishers are perfect for areas where appearance is important. Even the elegantly designed sStainless steel handles are now standard across this range.
It’s not just a beautifully designed extinguisher, stainless steel is one of the most corrosion-resistant metals available as well as being very strong – making these extinguishers amongst the toughest available. This makes them extremely practical and durable, lasting well in even the harshest of environments. The following extinguisher sizes and types are available for this range:
-
6ltr Water Stainless Steel Extinguisher
-
9ltr Water Stainless Steel Extinguisher
-
6ltr Foam Stainless Steel Extinguisher
-
9ltr Foam Stainless Steel Extinguisher
-
6ltr MultiChem Stainless Steel Extinguisher
-
2kg CO2 Polished Chrome Extinguisher
-
5kg CO2 Polished Chrome Extinguisher
-
6kg Powder Stainless Steel Extinguisher
-
9kg Powder Stainless Steel Extinguisher
Brushed Antique Copper Fire Extinguishers
If you are familiar with antique extinguishers you will know just how beautiful antique copper extinguishers are. Capturing the essence of those designs and finishes, these industry-first are hand-finished extinguishers
These extinguishers are perfect for modern bars and restaurants, luxury hotels, contemporary offices, period homes and much more, this is fire safety equipment you actually want people to see! Also available with matching brushed antique copper tubular stands and ID signs, this range is truly design elegance in Fire Defense. The following extinguisher sizes and types are available for this range:
-
6ltr Water Antique Copper Extinguisher
-
6ltr Foam Antique Copper Extinguisher
-
6ltr MultiChem Antique Copper Extinguisher
-
CO2 Polished Antique Copper Extinguisher
-
6kg Powder Antique Copper Extinguisher
For further information and pricing on this stunning range of hand finished, contemporary fire extinguishers please contact us.
Fire Safety Training
keeping employees safe from the danger of fire
What is fire health and safety training?
Fire health and safety training is a legal requirement enforced by the UK Fire Legislation which stipulates that all employers need to ensure that their employees have adequate fire safety knowledge and training for their working environment.
Our two main courses we offer are:
-
Essential Fire Safety Training
-
Fire Warden Training Course
Apart from the legal duty, it is also good practice to make sure that your employees are safe and know what to do in the event of a fire as this can prevent a small incident escalating or even save lives.
At Fire and Safety Solutions we are able to offer a range of fire health and safety training solutions, for companies large or small, from first time fire safety training though to refresher courses or bespoke training for your specific environment. As well as the theory, we also provide ‘hands on’ training with items such as fire extinguishers, showing the attendee’s the correct type and method for extinguishing fires.
Key Points:
-
Range of courses from basic fire safety awareness through to Fire Warden training
-
Hands on demonstration of equipment and their use, such as fire extinguishers
-
All courses meet the legal requirement for appropriate employee training
-
Keep employee’s safe from the risks posed by fire
At Fire and Safety Solutions all of our courses are bespoke to your needs. We have a core syllabus for each course and adapt this to meet your specific requirements, business type and environment.In addition to our two core courses below, if you require a fully bespoke course to meet very specific needs please contact us to discuss your course, we would be happy to help.
Essential Fire Safety Training
Throughout this training course, attendees will get a general understanding of what to do if there is a fire, how to reduce the risk of a fire occurring, plus a practical tutorial of tackling a fire with a fire extinguisher. The course also demonstrates what actions should be taken to keep yourself safe from fire and other people around them too.
How long is the course?:
The course last between 1.5 and 2 hours.
The course will cover the following:
-
What to do in the event of a fire
-
How to raise the alarm
-
What to do if you hear the fire alarm
-
Who is responsible for calling the emergency services
-
The location of extinguishers and escape routes
-
Assisting disabled people and evacuation procedures
-
Best ways to prevent a fire
-
Understanding how a fire spreads and reacts
-
Types of fire extinguishers and their uses
-
Practical demonstration of fire extinguishers and the most effect way to use them
How many people can attend the course at once?
The course is suitable for up to 15 people at any one time. This ensures that each participant get’s adequate ‘hands on’ training with equipment without leaving other others standing around for too long.
How often should the course be carried out?
We recommend that the course is carried out every 3 years.
Will I each participant get a training certificate?
Yes, each person who completes the course will get a Fire Safety Certificate to confirm their participation and completion of the course.
Are there any age restrictions?
No, at Fire and Safety Solutions Ltd we believe that people of all ages and ability should be shown what to do in case of a fire and effective ways of keeping themselves and others safe.
Where does the course take place?
Ideally the course should take place in the environment it applies to, e.g. your office. However, this is not always practical due to the nature of some of our clients businesses and in such circumstances we would arrange a suitable venue for you.
We also offer a more advance course as follows:
Fire Warden Training Course
This course covers all of the points of the essential fire safety course, however in addition we establish and focus on the duties of an appointed fire warden, what they are responsible for and what expectations are placed on this person. We will also establish a chain of command and run through theoretical situations of emergencies that could occur in your building type, asses how the fire warden responds and advise where more effective fire control and evacuation methods could be used.
Fire wardens are not only a practical aspect of fire safety, it is also written in law (The Regulatory Reform (Fire Safety) Order 2005) that you must have enough, trained and appointed fire wardens to perform evacuation procedures in an emergency situation. The number of fire wardens will vary depending on how many people you have in the building and the size of the building, a fire risk assessment would need to be carried out by Fire and Safety Solutions to determine the correct number of fire wardens.
How long is the course?:
The Fire Warden course lasts approximately 2.5 hours.
The course will cover the following:
-
What to do in the event of a fire
-
How to raise the alarm
-
What to do if you hear the fire alarm
-
Who is responsible for calling the emergency services
-
The location of extinguishers and escape routes
-
Assisting disabled people and evacuation procedures
-
Best ways to prevent a fire
-
Understanding how a fire spreads and reacts
-
Types of fire extinguishers and their uses
-
Practical demonstration of fire extinguishers and the most effect way to use them
-
Establish the duties of an appointed Fire Warden
-
Establish the Fire Warden is responsible for
-
Identify the expectations placed on the Fire Warden
-
Establish a chain of command
-
Run through theoretical situations of emergencies that could occur in your building type
-
Asses how the fire warden responds and discuss corrective actions
-
Advise where more effective fire control and evacuation methods could be used
How many people can attend the course at once?
The course is suitable for up to 15 people at any one time. This ensures that each participant get’s adequate ‘hands on’ training with equipment without leaving other others standing around for too long.
How often should the course be carried out?
As with the Essentials Fire Training we recommend that the course is carried out every 3 years.
Will I each participant get a training certificate?
Yes, each person who completes the Fire Wardens course will get a Fire Safety Certificate to confirm their participation and completion of the course.
Are there any age restrictions?
No, there are no age restrictions.
Where does the course take place?
Ideally the course should take place in the environment it applies to, e.g. your office. However, this is not always practical due to the nature of some of our clients businesses and in such circumstances we would arrange a suitable venue for you.
Courses are tailor made to your exact requirements but the UK Government sets out guideline specifications for Fire Safety Training. The types of equipment you need will vary depending on your premises. All fire safety equipment must be properly installed, tested and maintained and your staff will need to be trained how to use them if necessary.Staff should be trained on:
-
The correct use of fire extinguishers and the appropriate type of extinguisher to use
-
How to raise the alarm
-
Correct escape routes
-
How to spot defective safety equipment and who to report it too
Fire Alarms
a comprehensive range of fire alarms for all situations
Fire and Safety Solutions are able to offer a full range of fire alarms, suitable for a range of applications throughout Cambridgeshire and the whole of the UK, from conventional alarms to the very latest in wireless technology.
We offer the following Fire Alarm services:
-
Supply
-
Installation
-
Servicing (both ad hoc and maintenance contract)
-
Fault Finding
-
Survey/System Advice
Below is a selection of our fire alarms range, for full alarm details or to arrange a free fire safety survey to asses which alarm would be correct for your needs, please contact us.
Conventional Fire Alarms
a tried, tested and trusted conventional fire alarm solution
Below is a selection of our fire alarms range, for full alarm details or to arrange a free fire safety survey to asses which alarm would be correct for your needs, please contact us.
Conventional Alarms
Addressable Alarms
Wireless Alarms
EMS FireCell Wireless Alarms
EMS IRIS+ Personal Security Alarms
The most commonly installed fire alarms in businesses are either non addressable or addressable. A non addressable system is also commonly referred to as a conventional system.
Non addressable alarm system (Conventional)
Suitable generally for smaller businesses or properties. Devices are connected directly into a control panel via their own fire proof cable. If a cable is broken for any reason, then the device will stop working. For larger premises or on say 2 or more floors, devices can also be connected in Zones. E.g. Zone 1 ground floor, Zone 2 first floor. If a device activates due to smoke or fire then at least it would be possible to identify roughly where on your premises there is a fire.
Addressable alarm system
All devices such as smoke detectors or call points are linked back to a control panel via fire proof cable loop. If a device fails to work for any reason, the remainder will keep on working.
Every device connected to an addressable system has a unique address. When a fire is detected, the address is highlighted on the main control panel indicating which device has been activated. This indicates the precise location of a fire and enables a relevant fast safe response. This system could save a lot of valuable time finding a fire when compared to a non addressable system. This in turn can dramatically reduce possible fire damage, save your business or even lives!
An addressable system is more sophisticated and will reduce the number of false alarms, which are now charged for by the fire brigade.
What are Conventional Fire Alarms?
If you are looking for a simpler, reliable fire alarm system and you have a small building, then a conventional (non-addressable) fire alarm could be the solution. A conventional fire alarm allows you to have multiple detectors and sounders, each of which can be divided up in to zones. Unlike addressable fire alarms, each detector can not be identified individually so it does make a fire harder to locate, which is why this system is only suitable for smaller buildings.
Our conventional control panels allow you to test and monitor the function of the entire system. It will alert you to any potential problems with the sounders or detectors so you can arrange repairs or servicing as necessary, maintaining your complete protection. We offer conventional systems ranging from a 2 zone up to 16 zone.
At FASS we’re not beholden to any one manufacturer. As an independent Fire Safety specialist, we can supply, install and service all types of alarms across Cambridgeshire and the UK.
Addressable Fire Alarm Servicing
Fire and Safety Solutions Ltd offer a range of conventional fire alarm servicing and maintenance options to suit all types of business and premises. Most clients benefit from our service and maintenance contract which offers 24 hours a day, 7 days a week call out as well as regular, manufacturer defined servicing at the required intervals.
We also offer one off pay as you go alarm servicing for clients who do not wish to take out an ongoing contract. Plus we also provide one off fault finding for conventional alarms, please contact us for further information.
Key Features:
-
Cost effective on smaller installation (under 20 devices/detectors)
-
Tried and tested system
-
Most manufacturers devices are compatible with each other
-
Cost to purchase the hardware is less than more complex systems
-
Simple setup and usage
2 Year Guarantee
We are 100% confident in our products and services which is why our fire alarms come with a 2 year guarantee as standard for your complete peace of mind.
thumbs_20_lcmu_large thumbs_-fire-alarm-panel thumbs_Eclipse-B thumbs_New-Flush- Manual-Call-Point
thumbs_MCP1A- thumbs_Beacon-Red-Clear450 Sounder-Beacon-Red-Clear450 S1-Sounder-Red-2450 (1)
Y470SG-14-450a
thumbs_74432-88NM-450 thumbs_Way-input-output-card Optical-Smoke-Detector Remote-Test-Unit
thumbs_KFB6-450
Addressable Fire Alarms
comprehensive fire safety with precise fire location
What are Addressable Fire Alarms?
Addressable fire alarm systems are a step beyond the conventional fire alarm system. Using the addressable control panel, you can test and monitor the function of the entire system location by location. It will alert you to any potential problems with the sounders or detectors so you can arrange repairs or servicing as necessary, maintaining your complete protection.
Each addressable device (e.g. smoke detector) is identified individually by an address (ID) within the system. The control panel communicates with each device one by one and each device reports back a detection level of smoke or heat. If smoke or heat are detected, the control panel then sounds the alarm on the detector.
As each device is uniquely numbered it gives you the ability to pinpoint the location of the fire precisely giving you valuable time in evacuating the building as well as assisting your local fire service tackling the fire.
At FASS we’re not beholden to any one manufacturer. As an independent Fire Safety specialist, we can supply, install and service all types of alarms across Cambridgeshire and the UK.
Addressable Fire Alarm Servicing
Fire and Safety Solutions Ltd offer a range of addressable fire alarm servicing and maintenance options to suit all types of business and premises. Most clients benefit from our service and maintenance contract which offers 24 hours a day, 7 days a week call out as well as regular, manufacturer defined servicing at the required intervals.
We also offer one off pay as you go alarm servicing for clients who do not wish to take out an ongoing contract. Plus we also provide one off fault finding for addressable alarms, please contact us for further information.
Key Features:
-
Pin point accuracy on fire/smoke location
-
Ideally suited to larger/complex installations (e.g. more than 20 detectors)
-
Multiple control panels and circuits can be networked together to create one large detection system
-
Individual detectors can be isolated rather than all the detectors on that one loop
-
Reduced number of false alarms
-
Cheaper to install compared to equivalent conventional alarm
2 Year Guarantee
We are 100% confident in our products and services which is why our fire alarms come with a 2 year guarantee as standard for your complete peace of mind.
Wireless Fire Alarms
complete fire safety protection with hassle free installation
What are Wireless Fire Alarms?
Our Wireless range of fire alarms, smoke detector and heat detector products are the most technically advanced and innovative hybrid fire solutions currently available. We are able to supply, install and service wireless alarm systems across Cambridgeshire and throughout the UK.
The system has an impressive track record and is very popular with a wide range of customers due to it’s ease of installation and use. The system seamlessly integrates wired and wireless devices with industry standard control equipment (all conforming to European Standard EN54-25) to provide a cost effective solution for almost any application.
Due to the ease of installation and modular nature of wireless systems, they can be up or down scaled, or moved to a new location quickly and efficiently.
At FASS we’re not beholden to any one manufacturer. As an independent Fire Safety specialist, we can supply, install and service all types of alarms.
We work do however work closely with EMS FireCell and recommend this system as being an excellent quality, reliable and cost effective solution to our clients.
Please visit our dedicated EMS FireCell page for further information.
Wireless Fire Alarm Servicing
Fire and Safety Solutions Ltd offer a range of wireless fire alarm servicing and maintenance options to suit all types of business and premises. Most clients benefit from our service and maintenance contract which offers 24 hours a day, 7 days a week call out as well as regular, manufacturer defined servicing at the required intervals.
We also offer one off pay as you go alarm servicing for clients who do not wish to take out an ongoing contract. Plus we also provide one off fault finding for wireless alarms, please contact us for further information.
Key Features:
-
No cable runs or unsightly wires on show
-
Quicker and more flexible to install, minimising impact on your business
-
No disruption to the fabric of the building (especially relevant to historic buildings or those with contaminants such as Asbestos)
-
Ideal for sites/complexes with more than one building
-
Can be used a temporary system, e.g. exhibition/display or construction site
-
Ideal for use in refurbishment, historic or listed buildings
2 Year Guarantee
We are 100% confident in our products and services which is why our fire alarms come with a 2 year guarantee as standard for your complete peace of mind.
FireCell works by using a Hub and Cluster system which means it can be either a 100% wireless or a mixture of wirless and wired loops depending on the requirements. Using fire resistant cable, the Wireless Hub connects to the loop input/output of the CIE and each Hub can support up to four wireless loops.
Using this set-up, a system can be configured with both wired and wireless loops and a four loop CIE could, for example, have a single wireless loop with three hard wired loops.
A FireCell system can be single loop, two loop or four loop supporting up to 126 devices on each loop and 504 devices per panel (four loops). These can be wired or wireless devices depending on the requirements. Each loop must be dedicated as wired or wireless although Radio Loop Modules (RLMs) and can be added to the wired loop for localised wireless devices.
Larger systems, with up to eight panels, can be wirelessly networked using the EMS Radio Network Communicator (RNC) and support up to 4,032 devices.
The FireCell Radio Loop Module supports any combination of wireless devices up to a total of 31 loop addresses. The RLM itself will take up one additional loop address.
Each FireCell RLM is wired on to and powered directly from the loop. All wireless devices, including sounders, have their own power supplies (batteries) and do not need to be included in the loop loading calculations. Each hard wired loop can support a maximum of five RLMs.
Specifications vary depending on the type of system required. In order to obtain the correct specification for the system most relevant to your needs, please call our sales team to discuss your requirements.
EMS IRIS+ Wireless Alarm
wireless alarm for staff protection and personal attack situations
About EMS and the IRIS+ wireless alarm system
The EMS IRIS+ wireless alarm system is the most widely used wireless hi-integrity system for protection of staff and protection for personal attack situations. The IRIS+ system is industry leading and as such it is used by nearly all financial institutions throughout the UK.
Fire and Safety Solutions Ltd are able to supply and fit the wireless alarm system which is an extremely reliable and flexible, with multiple configuration options available making it suitable for nearly all applications. As it is wireless, the need for cable is eliminated and any additions or alterations can be made quickly and cost effectively.
The combination of replaceable low-cost energy packs in each unit, combined with system wide power management software also reduce the overall operating costs. The Transmitters do not require charging every day and each handset requires two AA alkaline batteries which should provide approximately 5 years of operating life based on typical usage.
IRIS+ uses a secure signalling system that eliminates false alarms from other radio interference and fault condition is reported immediately due to the transmitter call-in failure detection which is a standard feature of IRIS+.
The 7256 IRIS+ enables optional site wide paging using the EMS paging facility which allows managers and security staff to receive information at any location on the site.
FASS Recommended Wireless Alarms
At Fire and Safety Solutions we work with leading manufacturers for all of our products we supply and are happy to install or service most market leading brands.
With manufacturers who we feel exceed all of our expectations, we work closely with them in order to provide our customers with not only the best pricing but also access to the expertise and knowledge that manufacturer can offer, ensuring you get a premium product and service.
EMS IRIS+ wireless products are one such manufacturer who FASS endorse and recommend as a trusted supplier.
Key Features:
-
Extremely Flexible – Can be adapted to suit virtually any building where a personal attack risk is a threat. Workers on site alone can be vulnerable and wireless handsets ensure they are always able to call for assistance or raise the alarm should it be required
-
Cost Effective – IRIS+ can be easily modified as the building or risk change. This can be carried out quickly and without interruption to your business
2 Year Guarantee
We are 100% confident in our products and services which is why our fire alarms come with a 2 year guarantee as standard for your complete peace of mind.
The IRIS+ system consists of two key components, the 7256 IRIS Controller and the 7500 Alarm Device. In addition to this, you can also include the 7972 Pendant. Details of each component are as follows:
IRIS Controller
The IRIS wireless radio personal attack alarm system is designed for use in all types of financial, industrial or commercial buildings where staff need the security of an instant response personal attack alarm. The transmitters can also be placed in fixed positions and as it is wireless any changes can be made quickly and cost effectively. False alarms which were often caused by damage to traditional wiring circuits are totally removed.
The system can monitor up to 256 transmitters, each uniquely identified by the receiver. Every event is time and date stamped and stored in incident log which can be reviewed using the LCD screen. After resetting, the events are then archived to the historical log, which can also be read from the display or with an optional plug-in printer.
The IRIS personal attack receiver range includes a range of software features which enable you to manage activation’s if required e.g. alarm verification for high risk personnel (cashiers, early morning entry etc) and or low risk personal, such as financial services – this allows you to distinguish the groups as to if the police should attend or if local assistance is required. This can assist in reducing unwanted police call-outs.
The IRIS system fully complies with police requirements for confirmed alarms (BS8243:2010) and is designed to comply with EN50131 conforming for radio signalling.
Alarm Device
The main function of the transmitter is to provide portable protection, with a local assistance button and a dual action full alarm/panic facility.
Typical Applications:
-
Personnel protection/support – e.g. financial institutions, cash based operations etc.
-
Maintenance workers in hazardous areas.
-
Loan worker situations, where a base receiver can be connected to a remote signalling system, providing backup support.
-
Security guards, prison officers or nursing staff where duties are considered ‘high risk’
-
Unsupervised employees, lab staff, forklift truck drivers, warehousemen etc.
The 7500 also offers an additional safety feature – a man-down facility including an audible warning option. Following user activation, tactile verification is also available as an option. Visual indication is provided for both full activation and battery low monitoring.
The system is designed to comply with EN50131 conforming for radio signalling and fully complies with police requirements for confirmed alarms (BS8243:2010).
Pendant
The IRIS wireless pendant can be worn in different ways depending upon your own company requirements and is supplied with a “quick-release” lanyard as standard. This can be changed to one of your own branded lanyards should you require.
Each pendant has a battery life of 12 months based on typical usage and up to 256 pendants can be used with a single system. Using secure UHF frequencies, which typically allow in excess of 150 meter coverage from the IRIS panel, users are able to continue carrying out their work safe in the knowledge that help is on hand, should it be needed.
Using dual activation (large red buttons on each side of the pendant) to request assistance and eliminate any false activation’s, this pendant is a vital addition to your Health and Safety plan.
Each pendant is lightweight (only 25.35g) which makes it virtually “invisible” until such time it is needed.
Specifications vary depending on the type of system required. In order to obtain the correct specification for the system most relevant to your needs, please call our sales team to discuss your requirements.
Fire Safety Equipment & Signs
keeping you safe and informed
What do I need to know about fire health and safety signs?
At Fire & Safety Solutions we pride ourselves on providing high quality products and only sell what we assess either meets or exceeds the standard.
Each fire health and safety sign is designed so that it will glow in the dark, lasting for up to 30 hours, highlighting the key safety elements in the event of a power failure such as the fire exits and extinguishers locations.
We offer a variety of Fire Safety Products which include but are not limited to:
-
Fire exit signs
-
Assembly point signs
-
Fire Extinguisher ID signs
-
No smoking signs
-
Fire Blankets
-
Fire Extinguisher stands
Fire Safety Signs
Fire and Safety Solutions have an established partnership with Everlux, who are industry leaders in the production of high quality safety signs. Because of this strong relationship, we are able to offer our clients fire safety signs at very competitive prices without compromising on quality.
-
To find out more information or for a quote, please contact our sales team
All of our signs are in conformity to the following norms:
-
ISO 16069:2004
-
ISO 7010:3003
-
Norms ISO 3864
-
ISO 15370: 2001
-
IMO Resolution A:752(18)
-
Council Directive 2004/54/EEC
-
European Directive 92/58/CEE
-
Norms DIN 67510
-
BS 5499-4:2000
-
BS EN 3-5
-
BS 5266-6:1999
Most importantly we only sell Photoluminescent signs that either meet or exceed the British Standards.
-
Photoluminescent rigid plastic, 2 mm thickness, antistatic surface and easy to clean
-
Non inflammable, self-extinguishable



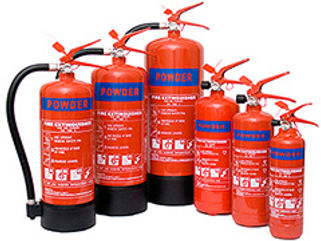
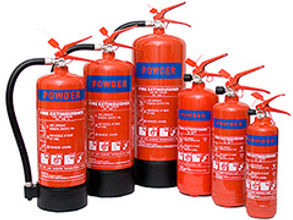

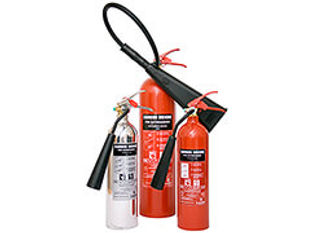
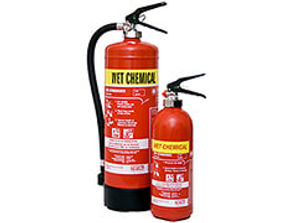


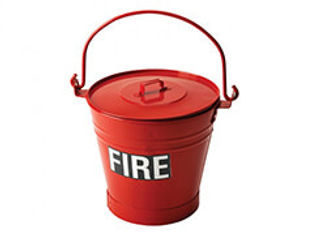
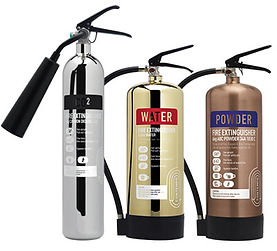



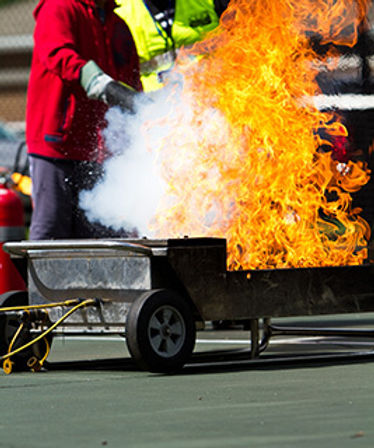
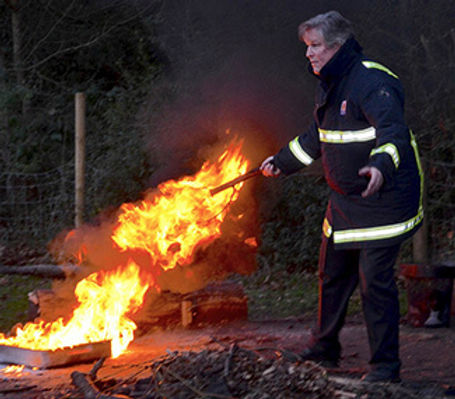
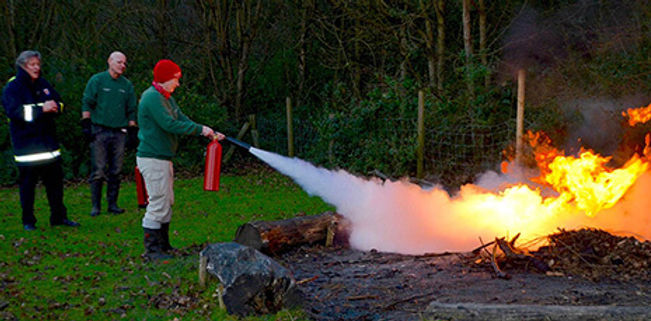




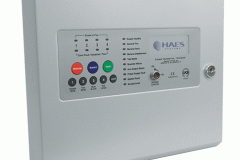


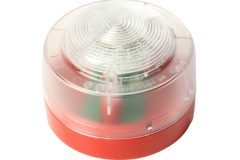



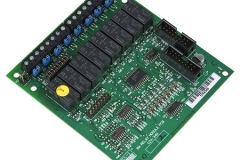



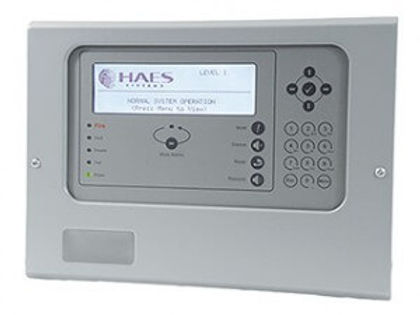

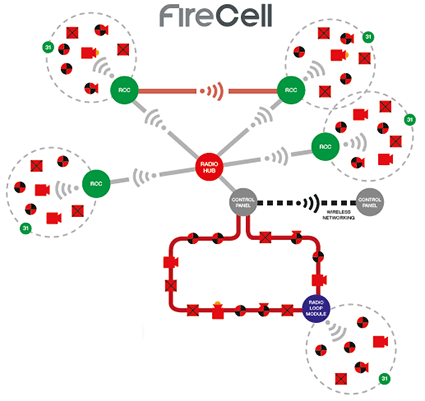







KENSTEVE OILFIELD AND ALLIED SERVICES NIGERIA LIMITED
KENSTEVE OILFIELD AND ALLIED SERVICES NIGERIA LIMITED IS REPRESENTING LEADING MANUFACTURERS IN FIRE PROTECTION & SECURITY.
We an Internationally Certified distribution organization part of a larger group is a specialist distributor of a wide range of fire extinguishers,other fire protection products.
When it’s time to choose the right Fire Protection Equipment Supplier for your business or home needs, you can count on Kensteve oilfield and allied services Nigeria limited for quality products that will fit your budget. We guarantee you receive only the best quality products delivered to you in no time and totally hassle free. Let us know what your organization or home are missing and we’ll take care of the rest.
KENSTEVEOILFIELD&ALLIEDSERVICES NIG.LTD. Was established to provide a broad new level of services in the distribution and Maintenance of Fire Fighting Materials and Equipements. Our Future is guaranteed by our extensive experience and solid performance with our clients in the past.
KENSTEVE OILFEILD & ALLIED SERVICES NIG LTD.(KOASNL) Have signed distributorship agreement with manufacturers of fire safety and oil spill protection,logistics materials/equipment and machineries located in USA, EUROPE, CANADA, AUSTRALIA, ASIA, & MIDDLE EAST.
Find below some of the said agreements and reputable manufactruers'products pages like Britannia fire at UK,NAFFCO/GERMANIA at DUBAI UAE,SpilTech Environmental in at USA,Innotex at CANADA,POK at FRANCE,Productos at SPAIN, Philip and Smith at NEWZELAND, Jacinto at PORTUGAL, just to mention a few.

Meet the Team
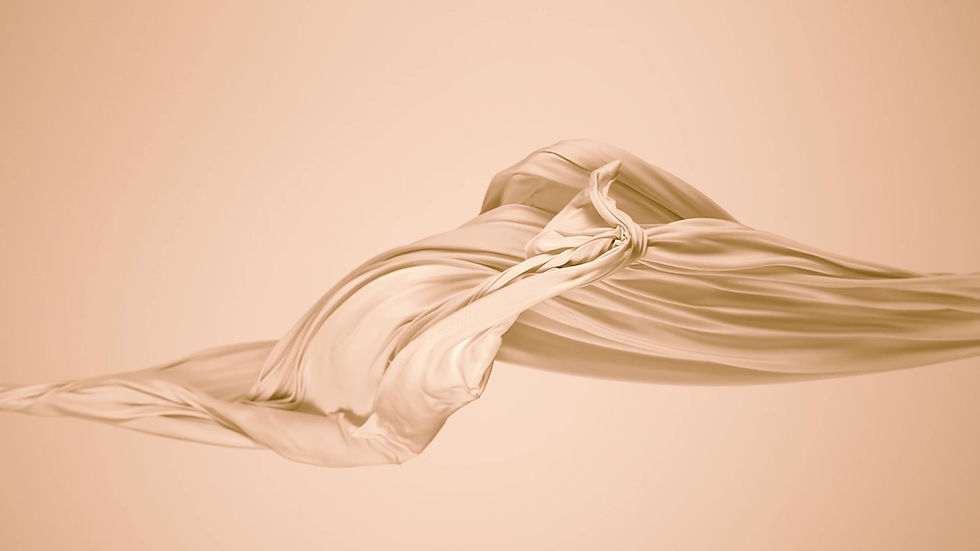

QUALITY MANAGEMENT MANUAL
Top Notch Products
1.0 Introduction
This Manual explains the means by which KENSTEVE OILFEILD & ALLIED SERVICES NIG LTD.(KOASNL) hereafter referred to as the Company, puts into practice its Quality System. The Company's Quality System complies with the requirements of the
International Standard BS EN ISO 9002. The Manual describes the
overall Quality Policy, its principles, organizational requirements and how the main Company activities are controlled. To satisfy specific contractual requirements, project Quality Plans shall be constructed to clearly identify and document the specified requirements. The Quality System is based on a documented system which consists of three levels. The first level is made up by the Quality Assurance Manual, this is a policy document which does not include procedures. Administrative Documents which specify the organizational basis of the system and Key Quality Management Procedures form the second level of Quality Documentation. The level consists of specific Operational Procedures and Work Instructions. For details of the specific procedures adopted throughout the operations of the Company to ensure that the required quality is achieved, reference should be made to second and third level documents. The Quality Assurance Manual and its supporting documentation are controlled documents. Copies of this Manual and the relevant sections of its supporting documentation shall be held by Managers at the level of Department Head and above, but shall be available to all employees. A Register of Holders shall be maintained by the Quality Assurance Department. Additional controlled copies can be issued to a department on written request from the Department Head. To support the Quality System, the Company shall maintain effective communication with the Client through the Operations and the Sales and Marketing Departments. A performance monitoring questionnaire will be sent to the Client on work completion, in order to determine his perception of the quality of the service provided.
2. 0 ORGANISATION
An Organogram of the management organization is given Appendix 1.
2.1 individual Responsibilities the Managing Director has overall responsibility for the existence of the Quality System. The Quality Assurance Manager reports to the Managing Director and as the appointed management representative he is responsible for the control and administration of the requirements of the Quality System. The individual responsibilities of key personnel are defined in the job descriptions given in the departmental administration procedures contained in the Quality Assurance Level Two Documentation.
2.2 Departmental Responsibilities A brief resume of the departmental responsibilities is given below
SAFETY
To provide professional safety advice and assistance and to monitor the adherence to safety and environmental requirements through the Safety Officers and the Radiation Protection Advisor.
QUALITY ASSURANCE Responsible for the administration of the Quality System including monitoring its effectiveness.
FINANCE AND ADMINISTRATION Responsible for personnel recruitment, office equipment and routines, central document control, purchasing, subcontracting, accounting, invoicing, cost control, building maintenance and warehousing.
BUSINESS DEVELOMENT /COMMERCIAL UNIT Responsible for the compilation of tender submission to Clients and the review and control of contracts.
MARKETING AND SALES Responsible for promoting the Company, development of marketing and sales strategy, analysis and review of customer requirements and the investigation of new or alternative markets for the Company’s services.
OPERATIONS
Responsible for the mobilisation, operation and logistical support for the Services.
EQUIPMENT AND MAINTENANCE
Responsible for the maintenance, calibration and certification of all the Company’s equipment.
MATERIALS/LOGISTICS
Responsible for the purchasing of all Company equipment and consumables and for the movement of all Company equipment resources.
TECHNICAL Responsible for design, engineering, technical, inspection, planning and Drawing Office services and support for departments and other offices as required.
PERSONNEL Responsible for the aspects of personnel administration and recruitment for all permanent staff and benefit administration for sub-contract staff.
2.3 Resources Each department shall identify the necessary verification requirements for its activities and shall allocate adequate resources and personnel to ensure that these requirements are demonstrably completed by inspection, review, or audit.
3.0 QUALITY SYSTEM
3.1 Core Quality System KENSTEVE OILFEILD & ALLIED SERVICES NIG LTD.(KOASNL) has established a documented Quality System as a means of ensuring that its products and services conform to specified requirements. The Quality System includes the provision of a Quality Assurance Manual, documented Operational Procedures and Work Instructions and a document control system. Other critical factors in the Company‘s Quality System include the development, acquisition and review of those components necessary to achieve required quality, the clarification of standards of acceptability, the compatibility of activities and documentation and the identification and preparation of quality records. A schematic representation of the Quality Assurance System documentation is contained in Appendix 2. Quality Procedures and Work Instructions are written within the relevant Departments, reviewed by other involved Departments where necessary and authorized by the Manager or Head of the relevant Department before being issued by the Quality Assurance Department. Quality Assurance staff are available to evaluate these Procedures and Work Instructions to ensure adherence to Quality Assurance Principles.
3.2 PROJECT QUALITY SYSTEM
Each project undertaken by the Company shall have Project specific documentation prepared in accordance with the Standard System in order to ensure that all relevant information is available to personnel at the work site. Quality Plans shall be developed which reference to all applicable project and generic Company procedures. Wherever possible, Procedures and work Instructions from the Core Quality System shall be used with appropriate bridging documents to modify them so that they accurately reflect the project procedural requirements identified and evaluated during contract review.
Where required, the Procedures shall be collated in a Project manual. The preparation of this Manual shall be the responsibility of the assigned Project Manager,
3.3 Management Review
A review of the Quality System shall be undertaken by the Managing Director, at nominal intervals of six months. The review meeting may be incorporated into other meetings held by The Company‘s senior management. Additional meetings may be held where a significant impact on the Quality System arises. The review is carried out to determine the continued suitability and effectiveness of the Quality System and the achievement of quality objectives. The results of the review shall be minute and the Development Plan prepared as a result of the review shall be circulated.
4.0 CONTRACT REVIEW Upon the receipt of any Tenders for contracts, it is essential that documented Contract Reviews take place. This review is the responsibility of the Business Development/Commercial Unit Upon receipt of an enquiry, an initial review is carried out to determine the Company's capability to comply with the Client's requirements. The responsible department will agree to submit an offer (bid). In order to prepare the bid, an in-depth review of the contract requirements is carried out from both technical and commercial standpoints.
On award of the contract, and prior to its acceptance, a detailed review of all contract documents is carried out to ensure that its requirements are the same as those of the tender, any areas differing from those in the tender shall be resolved.
Procedures are documented to ensure that the requirements of the contract are defined and documented so that any' requirements differing from those in the tender can be resolved in a timely manner. Procedures exist to ensure that input is received from members of the Company with experience in relevant fields, thereby ensuring that the Company has the means to meet agreed contractual requirements.
Project Managers and other personnel are available from all Departments. of the Company to ensure that appropriate input to the Contract Review is obtained at both the Tender Submission and Contract Award phases. Any variation from the original tender enquiry shall be documented and resolved with the Client prior to contract acceptance. Where a variation arises after contract award, it shall be documented and implemented by the Project Manager, in accordance with the procedure documented within the contract. Records of these reviews shall be maintained in the Commercial Department.
Telephone requests or contacts for work, taken primarily by KENSTEVE OILFEILD & ALLIED SERVICES NIG LTD.(KOASNL) shall be verified prior to acceptance. This will be performed verbally by repeating the work request to confirm its requirements. A notation shall be made of the request in the Operations Diary/Logbook.
5.0 DESIGN CONTROL
5.1 General
The Engineering Department is responsible for the control and verification of all design work. This responsibility includes preparation, control, manning and review of the programed for each design or development activity. These activities shall be performed by suitably qualified and experienced personnel. Procedures are in place to identify the interfaces between different activities and to ensure that all essential information is documented, transmitted and updated as required. These procedures include those Interdisciplinary Checks required to minimize the possibility of inter-discipline conflicts and to ensure the efficient transmittal of information required to avoid duplication.
5.2 Design input
At the initiation of design work by the Engineering Department, input requirements are documented and reviewed by the Departments staff and key personnel from other relevant departments or Operations, to ensure the resolution of any incomplete, ambiguous or conflicting requirements.
This review covers input from within the Company as well as from the Client and Statutory requirements. Design work is carried out in accordance with those Codes or Standards specified by the Client, or, where these are not specified, in accordance with appropriate international Codes and Standards.
5.3 Design Output All design output is documented in terms of requirements, calculations, analyses, reports, logs, plans, etc. All output is reviewed by qualified and experienced staff to ensure that it meets design input requirements and contains all the characteristics critical to the safe and proper functioning of the finished product or service. This review is indicated by the signature of the reviewer on the relevant output document.
5.4 Design Review at each stage of design, a formal review shall be undertaken against the design brief to identify and anticipate problem areas and inadequacies and to initiate the necessary corrective actions.
5.5 Design and Development Planning
The Engineering Department is responsible for ensuring that all the stages of each design and development are documented and responsibilities for all activities are clearly identified, defined and allocated to suitably qualified and experienced personnel A design plan shall be developed and will conform to the requirements of the relevant procedures. In particular, it will define the project organization, the authorities and responsibilities of the project team, the design schedule, the control requirements in terms of interface, change and documentation controls and the method of verifying the design. These plans are updated as design progresses.
5.6 Design Verification
Verification of design work is performed to ensure that the design output meets the design input requirements and is carried out by suitably qualified and experienced personnel who, wherever practicable, are not directly involved in the design being assessed. Documents to be checked include calculations, drawings, procedures, etc. Such checks are documented by the presence of signatures of the personnel performing the checks. Where necessary, documented interdisciplinary Checks are arranged to ensure that all relevant interfaces between different disciplines are documented and any Non-conformances or conflicts are resolved.
5.7 Design Validation
A design validation shall be performed by means of appropriate tests and/or trials on the completed design to ensure that it conforms to the specified requirements
5.8 Design Changes Design changes shall be authorized, controlled and documented by implementation of the appropriate procedures otherwise Known as Management of Changes(MOC)
5.9 Records
All documents including the design plan, check prints, records of design review and other methods of verification, shall be retained and tiled systematically to enable the design and its development to be tracked.
5.10 Design Innovation The development of a design which is innovative in its approach to solving a problem by virtue of the use of new materials or techniques, shall be subject to a detailed design review, before it is adopted. Particular attention shall be paid to analysis of the risks involved relating to safety, feasibility, maintainability and reliability. Where an innovative approach is adopted, measures shall be taken to monitor the in-service performance of the product so that the product can be recalled if necessary.
6.0 DOCUMENT AND DATA CONTROL
6.1 Generality is Company Policy that systems for the generation, issue and control of all significant documents are operated to ensure that only the applicable issues of the relevant documents are available and used. Holders of Quality Procedures are responsible for complying with the procedures for the control of documents. They shall ensure that the pertinent issues of relevant Quality Procedures are available at all locations where operations essential to the effective functioning of the Quality System are performed. They shall also ensure that obsolete documents are promptly removed from all points of use by the personnel responsible for those procedures and that the OA Department is notified of any changes made to documentation. Similar controls are in use on projects to control incoming and outgoing documents.
6.2 Document Changes All documents contained in the Quality System are subject to annual review. Where this review indicates that change is required, the changes shall be made by the department to which they refer, in accordance with documented procedures. Documents shall be reissued when a significant number of changes have been made.
6 3 Technical Standards
Technical Standards required in association with the Companys operations are maintained current in the relevant Branch Library. Technical Standards not maintained current shall be suitably annotated.
6.4 Quality Related Documentation Quality related documentation e.g., drawings, inspection reports, etc., shall be issued and controlled in accordance with the document control procedure.
6.5 Electronic Data Control
Electronic data is controlled in a similar manner to those described above for documentation. Access to the Network is restricted to predefined users through the use of individual
passwords. The access is restricted to their departmental
directories and their individual directories.
7.0 PURCHASING
7.1 General
The objective of the Company’s policy is to ensure that all quality and safety critical products purchased conform to the requirements specified by the Company.
7.2 Evaluation of Subcontractors/Suppliers
Company Policy dictates that no Subcontractor/Supplier shall be used unless they have been evaluated (Subcontractor) or assessed (Supplier). Subcontractors/suppliers are assessed in accordance with documented procedures by means of audits, Third Party Certification and/or previously demonstrated capability and performance.
The type and extent of control exercised on subcontractors/suppliers is dependent on the criticality of the service in terms of its relevance to the Quality System. Where a supplier is found not to be meeting the quality requirements placed upon him by the Company, suitable corrective action shall be taken to resolve the problem.
Where persistent problems occur without remedial action being taken, the supplier shall be suspended and removed from the Approved Suppliers List. Where requested, the Client shall be allowed to verify a subcontractors work at their own premises, such verification by the Client does not absolve the subcontractor of his responsibility to meet specified requirements.
Under normal circumstances, operations will be under the direct control of the organization and management systems described above. In exceptional circumstances, when it becomes necessary to sub-contract NDT or other Technical Services, the use of the subcontractor is to be strictly controlled. Wherever practicable, priority will be given to the use of Certified Companies.
Where individuals are taken on contract, they will, for the purpose of operational control, be treated as and subject to, the same quality disciplines as permanent Company employees.
7.3 Purchasing Data
Controlled procedures ensure that all Material Requisitions and Purchase Orders are correctly completed, reveled and authorized before being processed. Once correctly completed, each form has sufficient information to clearly identify the materiel and the quality requirements. Where required, verification that the purchased product conforms to the requirements specified by the Company may be carried out in one of two ways; either by verification at source, or upon receipt of product. Such verification by the Company does not absolve the supplier of his responsibility to meet specified requirements.
8.0 CONTROL OF CUSTOMER SUPPLIED PRODUCT
In general, the Company does not use materiel supplied by the Client in the course of its normal operations. In cases WITSFE material is supplied by the Client for incorporation into a contract, it shall be controlled in accordance with documented procedures. Where this material is found, on receipt, during storage or use, to be deficient, damaged, unsuitable for use, or lost, the details shall be promptly recorded and reported to the Client for resolution. Where appropriate, this will be undertaken in accordance with the relevant contract requirements.
9.0 PRODUCT IDENTIFICATION AND TRACEABILITY
It is Company Policy that recognized identification shall be used. This identification is normally the Client's own identification for the items on which work is being performed. This identification is transferred to all relevant documentation generated during the work. All Company equipment is identifiable by its Asset Number or Serial Number. V\/here components are manufactured for incorporation into existing equipment, the Asset Number shall be used as a reference for traceability purposes.
Procedures are in operation which ensures that equipment and, where applicable, material can be directly related to their test certificates/reports.
10.0 PROCESS CONTROL
All production, maintenance, installation and inspection processes are performed in accordance with documented procedures under controlled conditions.
10.1 General
Wherever possible, core Quality System Documentation is used, with bridging documentation provided where necessary, to link the documentation to specific projects.
10.2 Special Processes
The nature of the Company‘s business involves the use of processes which are normally considered special processes, these processes are therefore considered as core business. Where special processes are required they will be performed in accordance with documented procedures.
11.0 INSPECTION AND TESTING
11.1 Receiving inspection - Goods
It is Company Procedure that all incoming goods are inspected or otherwise checked, on arrival at Stores Department, to ensure that all incoming goods conform to the specified Duality requirements. Those items rejected on receipt are identified as such and processed in accordance with the non- conformances procedure. The release of items whose quality is unproven is only permitted for urgent operational requirements. These items are identified in a positive manner and recorded so as to permit immediate recall and replacement in the event of subsequent non-conformances to the specified requirements.
11.2 Receiving Inspection - Off Hire All equipment being returned to the Stores or relevant operational department shall be inspected or otherwise checked on arrival at the Stores Department or relevant operational department, to ensure that the equipment is in good condition, complete and where required fully operational.
11.3 In-Service inspection Equipment which has been identified in the maintenance schedules by Statutory Legislation as requiring inspection or monitoring shall be inspected at the prescribed frequency and in accordance with the relevant procedure. Equipment failing these inspections will be suitably identified and quarantined until the necessary corrective actions have been completed.
11.4 Final Inspection
Where required by documented procedures or Quality Plans, products shall be inspected in accordance with documented procedures.
11.5 Inspection Records
Records are established and maintained to substantiate all inspections and tests performed. The records provide evidence of product quality and testify directly or indirectly that it is in compliance with specification requirements. Inspection and test records shall be legible, dated, clean, readily identifiable and include product identification, acceptance criteria, the nature and number of observations made, the inspectors name and the results obtained. The results shall include the number of conforming items, the number rejected and the cause or reason for rejection. Records of such activities are maintained for six years, unless otherwise specified by the Client.
12.0 CONTROL OF INSPECTION, MEASURING AND TEST EQUIPMENT
12.1 General The Company uses a wide range of inspection, test and measuring equipment in the services it provides with the exception of simple and rugged equipment e.g. steel tapes and rules, which are used as indicators rather than for precise measurement, equipment used for measuring purposes is uniquely identified and checked in-house for damage, readability and wear. All other inspection, measuring and test equipment is calibrated based on the requirement of the relevant National or international Standard prior to its operational use. Because some equipment is infrequently used, it is Company Policy not to maintain current the calibration/certification status of a given item of equipment whilst it is not in use.
12.2 Control register of all equipment in use which requires calibration is maintained. Calibration is conducted against certified equipment by a Certified Calibration Service Company or in accordance with a documented procedure. Calibration procedures shall ensure that calibrations are performed under suitable environmental conditions. Prior to the due date for the equipment recalibration, the Equipment Manager shall arrange for the instrument to be recalibrated in accordance with the appropriate National or international Standard which applies to the equipment.
The reference standards against which the equipment is calibrated must be traceable to a nationally or internationally recognized calibration source. Equipment shall be suitably labeled to indicate its calibration
status.
All measuring equipment shall be handled, stored and transported carefully and under conditions, compatible with their vulnerability and correct operation. When Client's or Subcontractor ‘s inspection, measuring or test equipment is to be used, it is the responsibility of the Company‘s personnel using the equipment to verify that the equipment is suitably calibrated prior to its use. Where the equipment has been transferred to Area Offices (Overseas), the responsibility for the control of calibration of inspection, measuring and test equipment is transferred to the Area Manager. The Area Manager shall ensure that the equipment is calibrated in accordance with the relevant National Standards. Procedures have been raised which define the responsibilities for the maintenance of calibration records. Where appropriate, safeguards shall be implemented to prevent inadvertent adjustments which would affect calibration accuracy. Should any inspection, measuring or test equipment be found to be out of calibration, a documented assessment shall be made of the affect on the validity of previous inspection and test results.
13.0 INSPECTION AND TEST STATUS The inspection/test status of the Company's equipment is clearly identified. The methods used to identify the equipment are defined and documented in Company Procedures. In all relevant departments, written procedures dictate that the inspection and test status of critical items, including welded or fabricated items shall, wherever practicable, be clearly marked and maintained through all stages of production and installation.
14.0 CONTROL OF NON-CONFORNIING PRODUCTS AND SERVICES
14.1 General
Materials, products or services which do not conform to specified requirements shall be clearly identified and where practicable, segregated to ensure that their use or installation is prevented until the nonconformity has been resolved in accordance with written procedures. The responsibility for review of and authority for the disposition of non-conforming products lies with the relevant Project Manager or Department Head and the Quality Assurance Department. The review of nonconforming product shall also take into account the activities prior to the discovery of the none conformance.
14.2 Nonconformity and Disposition Nonconforming products shall be reviewed in accordance with the documented procedures which indicate a review to determine trends and recurring problem areas. As a result of this review nonconforming items may be re-worked to meet specific requirements) Accepted with or without repair by concession) re-graded for alternative applications) rejected or scrapped Reworked and/or repaired items shall be re-inspected for compliance with the initial criteria unless otherwise agreed. Contractual obligations to obtain a concession from the Client using the Site Query proforma shall be upheld. A record shall be maintained by the relevant department of the actual condition of the item. The Quality Assurance Manager shall retain all records of Non-conformances and customer complaints and will carry out periodic reviews in order to analyze for trends which may develop.
15.0 CORRECTIVE AND PREVENTIVE ACTION
15.1 General The Corrective Action Procedure defines the requirement for investigating, identifying, evaluating and resolving causes of actual or potential nonconforming product. All non-compliances with documented procedures shall be documented, recorded and resolved. The Quality Assurance Department shall, where necessary, monitor inspection reports, concession applications, quality records and audit reports to detect potential causes of nonconforming product so as to determine the course of action required to prevent the recurrence of non-conformances Once suitable corrective action has been implemented, its effectiveness shall be evaluated by review or by other suitable means.
5 2 Customer Complaints
Customer complaints shall be recorded and promptly investigated. The findings of the investigation and the actions taken are formally reported to the Managing Director and customer.
15.3 Records
Records of corrective action including actions taken to resolve Non conformances and customer complaints shall be maintained for review and approval purposes.
16.0 HANDLING, STORAGE, PACKAGING, PRESERVATION AND DELIVERY
16.1 General
Procedures for the Materials Department define the requirements for handling, storage, packaging and delivery of goods and equipment to ensure that they are handled, stored and dispatched in such a manner that the risk of damage or deterioration is minimized during transportation Similar documented procedures exist to control electronic data.
16.2 Storage and Preservation
A Secure designated storage areas are provided on Company premises for the storage of goods and equipment. The Stores Department is responsible for the control of items in these areas. Where goods are subject to deterioration e.g. oil seals, or limited shelf life e.g. film, these items shall be subject to stock rotation and limited stock levels to minimize the storage period.
16.3 Handling
Care shall be taken in the selection and use of lifting equipment to ensure damage does not occur when equipment/consumables are dispatched to or returned from a work site.
16.4 Packaging and Delivery
Suitable containers, pallets and protective materials shall be used for protection purposes so as to minimize movement during transit. The Materials Controller shall ensure that all shipments conform to the Company, courier and customer ‘s requirements. Any hazardous goods shall be clearly identified and be accompanied by the relevant Safety Data Sheets.
When subcontractors are used for packaging, marking and delivery, they shall be fully instructed on the type and methods to be used to ensure compliance with the Client's requirements, or to ensure that the materials arrive in a satisfactory condition.
17.0 CONTROL OF QUALITY RECORDS records are maintained of all quality related activities, either as hard copy or as electronic data, to demonstrate the effectiveness of the Quality System, a documented procedure describes how these activities are performed. The records, shall be maintained for a period of six years unless otherwise specified by the Client. The manner of storage shall provide for the maximum protection from damage, loss or deterioration and allow suitable access for retrieval. Electronic data is automatically archived when a data file has not been accessed for two years. All contract/project related documents are identified by a unique reference number. The documents are filed in a documented system which allows for ready retrieval. Original and copy documents relating to a Client's project, whether generated by the Client, Supplier or the Company, will be filed in the system for a minimum of 6 years, thereafter, they may be destroyed at the Company‘s discretion unless the Client specifies a longer period of retention. The manner of storage shall provide for the maximum protection from damage, loss or deterioration. Personnel and Training Records shall be uniquely identified and retained by the Personnel Department for a period of a minimum of one year after the individual has left the Company.
8.0 INTERNAL QUALITY AUDITS
Internal Quality Audits are performed to monitor the effectiveness of the Quality System. All areas and activities that have an affect on the product or service quality are audited to verify their continued effectiveness or the need for change. Internal Quality audits are carried out in accordance with a documented procedure and to an audit programed by personnel who are independent of the area or activity being audited.
The results of each audit are documented and circulated to the management of the area or activity being audited, the Departmental Head and to the Managing Director. Corrective action agreed or required is also recorded and the effectiveness of its implementation verified. Failure to respond to the agreed or required corrective action is reported to the managing Director. The audit programme is adjusted on the basis of previous results. The importance of the activity is also taken into account. Auditors shall be trained and qualified for the audit tasks to be performed and so far as is reasonably practicable, they will have no direct responsibility in the areas being audited.
9 .0 TRAINING It is the policy of the Company to ensure that key personnel have experience and recognized qualifications appropriate to their assigned duties. A documented procedure describes how the training policy is put into effect. Departmental managers are responsible for ensuring that personnel either possess appropriate qualifications or are given access to training to ensure that they can obtain appropriate qualifications, these qualifications may be external examination or the result of in-house training schemes. The training requirements and Personnel Development Programme are established at the Management Review meeting. The Company's personnel are the key to ensuring that the Company maintains its high quality service. All personnel will, prior to employment, be vetted by the Personnel and/or Operations Departments and shall be competent and qualified to conduct the tasks assigned to them. Where appropriate, personnel will hold qualifications of competency issued through recognized bodies and/or will have extensive experience in their field of expertise, Qualifications and experience records of Company personnel are held on file in the Operations Departments or at the appropriate Area Offices and are available for review by Clients. When requested by a Client, qualifications and experience records will be submitted for review and approval. The qualifications of Operational personnel will be monitored through the use of the Personal Appraisal Programme and the results reviewed to identify any training needs. The Company provides instruction in the Safety and Quality Management Systems and the management principles embodied in them as part of the employee induction programme.
20.0 SERVICING Due to the nature of its business, the company does provide after-sales service facilities equipped with a mobile services delivery and maintenance van and qualified personnel.
21.0 STATISTICAL TECHNIQUES
The Company is not normally engaged in work of high volume, batch production or where the manufacture of many items with similar characteristics or processes is undertaken. In the event of the Company having a requirement for the application of statistical techniques, the necessary procedures will be developed and applied in accordance with recognized national standards.
KENSTEVE OILFEILD & ALLIED SERVICES NIG LTD.(KOASNL) strive for excellence in every facet of our corporate operation.
KENSTEVE OILFEILD & ALLIED SERVICES NIG LTD.(KOASNL) is a collection of principles, techniques, processes, and best practices that over time have been proven effective.
KENSTEVE OILFEILD & ALLIED SERVICES NIG LTD.(KOASNL) exhibits the majority of products, and services that are typically identified and required by Nigerian industries, Oil and Gas companies.
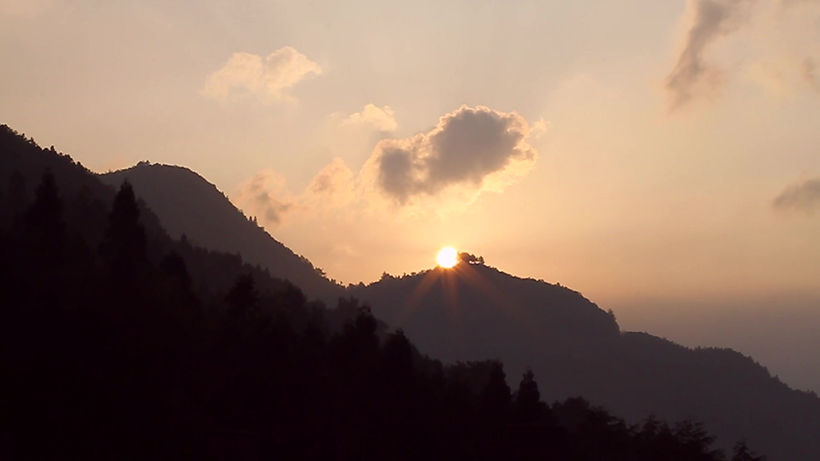
SERVICES WE OFFER
We’re a full service supply company providing our clients with a wide range of high quality products from trusted sources. All of the services and products we supply are produced in reputable factories and are backed by the Kensteve oilfield and allied services Nigeria limited name. Let us supply you with top notch service at a price you can afford.

FIRE EXTINGUISHERS MAINTENANCE
Guaranteed Precision
IMPORTANCE OF FIRE SAFETY EQUIPMENT SERVICING & MAINTENANCE;
We deal on all kinds of Fire extinguisher, portable or movable apparatus used to put out a small fire by directing onto it a substance that cools the burning material, deprives the flame of oxygen, or interferes with the chemical reactions occurring in the flame.
KENSTEVE OILFIELD AND ALLIED SERVICES NIGERIA LIMITED Having your premises kitted out with the requisite fire safety equipment helps to protect both your site as well as the people in and around it. But while having these individual pieces of equipment fitted is a great start, looking after the safety of your building is an ongoing task which you shouldn’t just ignore.
Put off by the cost of servicing and maintenance for fire safety equipment, it often boils down to one simple point: if you don’t have them serviced, why bother having them? While the odds may feel slim that a fire extinguisher will malfunction, it could end up costing you tens of thousands of Naira – or worse, a life – if a fault does happen to occur just as you need it to tackle a fire.
With this in mind, take a look at our guide to the most common fire safety equipment faults and their consequences to highlight the importance of fire safety equipment servicing.
FIRE ALARMS
What they’re for – Fire alarms are great warning systems to alert whole buildings to the possibility of a fire. By alerting people early, it allows everyone to file out safely to a designated point and await the assistance of the fire services. Fire alarms are a legal requirement for commercial premises but there is little emphasis placed on the upkeep of the system.
Common faults – Many faults for alarm systems involve power failures, requiring a system to be reset, but ground faults can also put the system out of action by knocking out the power to certain circuits. Also, a rare occurrence, but if your premises sustain water damage this could knock out your system if the water manages to encroach on the circuits.
Why we service them? – While many systems will have a control panel to tell you when there has been a fault, you may be unaware of a circuit which has been lost or the system may not spot the fault itself. A professional will be able to test the system fully to illuminate any hidden faults which may have developed, especially key if you have a building filled with alarm points to look after.
FIRE SUPPRESSION SYSTEMS
What they’re for – Automatic fire suppression systems are the ultimate way to tackle fires, triggering within seconds of the heat rupturing a trace tube. These can be fitted as direct or indirect systems and require no manual input or mains connection.
Common faults – With very little electronic equipment attached to the system and no human input required, fire suppression systems are less likely to develop faults. However, it could be that the suppressant simply needs topping up or that a part has become damaged and needs repair.
Why service them? – Not servicing your suppression systems renders them utterly pointless, as you’ll never know whether they are going to work or not. You need to have full confidence in your systems and this is something which requires professional attention.
FIRE DOORS
What they’re for – Fire doors are specially designed doors which help to contain fires when they break out, allowing people to make their escape and confine fire damage to as small an area as possible.
Common faults – Whether a door has become jammed, the seals are missing or the hinges haven’t been fitted correctly, there is a lot which can go wrong with a fire door.
Why service them? – According to The Fire Door Inspection Scheme survey, 677 fire doors across 31 premises had faults, highlighting just how bad things are. Having your doors inspected may only take a matter of minutes, but you’ll then have the peace of mind that they’ll do their job properly should the worst happen.
SPRINKLER SYSTEMS
What they’re for – A sprinkler system will erupt via individual points when they detect the heat of a fire, although not all at once. This then releases water into that area in the hope that the water will not only tackle the blaze, but also dampen the surrounding area to prevent it spreading.
Common faults – There are many things which can impact the performance of a sprinkler system, particularly if it sits unused for years on end – pressure being of particular importance here. Rust is one of the most common causes of faults for the components, along with the water in the system freezing and causing pipes to burst.
Why service them? – Having a sprinkler system checked over will highlight any issues and any parts which might need replacing. With a system check you can be assured that it will kick in when it is needed most rather than letting you down.
EMERGENCY LIGHTING
What it’s for – When a building experiences a fire it may cut the power to the building, in this instance, the emergency lighting kicks in to light the way out of the building for anyone left inside.
Common faults – A battery powered piece of equipment, one of the most common faults for emergency lighting not working is dead batteries. If not the batteries then the lamps themselves could be at fault, leaving people in the dark.
Why service it? – Nobody wants to be left stuck in a dark warehouse or corridor when the power goes out for any reason. Servicing emergency lighting ensures people can find the exit in an emergency, something which could save lives and avoid injuries.
FIRE EXTINGUISHERS
What they’re for – We all know how fire extinguishers can help tackle a flame while it’s still in a controllable state, but many people aren’t aware that there are different types of extinguishers for different types of fire, e.g flammable liquids, electrical fires, solids fires. These should be used to tackle a small fire to stop it spreading.
Common faults – Fire extinguishers are usually sitting around for years on end before use, leaving them prone to rusting and weakening. In addition to this, you may not realise when someone has tampered with an extinguisher, releasing the contents and turning it into a dud when someone actually needs it.
Why service them? – Fire extinguishers should be serviced by a BAFE approved company to guarantee they have been inspected by a certified engineer. By servicing and maintaining all the different extinguishers you have on site you can ensure the safety of your staff, visitors and your premises.
THE REGULATION GAP
Since 2012, it’s been down to the building manager or employer to take care of fire safety in a building. This responsibility has been taken away from officials, but this has proven to be dangerous in most cases with standards slipping in terms of fire safety.
The transfer of responsibility has already cost lives, with the hotel industry showing a distinct lack of effort in servicing and maintenance of fire safety equipment. In 2013 the Royal paradise hotel was engulfed by flames, costing three lives. The owners were handed a fine for this as well as for failing to meet safety standards. Meanwhile, a hotel in Abuja also saw the loss of a life, resulting in yet more calls for better safety laws.
Currently, businesses are not under any real scrutiny to uphold the standards which would see regular servicing and maintenance of all fire safety equipment, with many either forgetting or simply trying to save on the cost.
KENSTEVE OILFIELD AND ALLIED SERVICES NIGERIA LIMITED carry out fire risk assessments and have servicing and maintenance checks on a regular basis for all fire safety equipment.
FIRE SUPPRESSION SERVICE & MAINTENANCE
At Fireward, we not only supply and install fire suppression systems, we service and maintain them too. There is little point in investing in safety equipment if you’re not going to have them inspected at regular intervals to ensure they remain in top condition.
Whatever industry you operate in, it’s vital to make fire safety a top priority.
KENSTEVEOILFIELD AND ALLIED SERVICES NIGERIA LIMITED makes all this fore safety equipment and Oil spill absorbent Materials available to your organisations anywere in the country.
To learn more about our servicing and maintenance options for fire suppression systems, simply contact our professional team today and we’ll be happy to discuss your requirements.
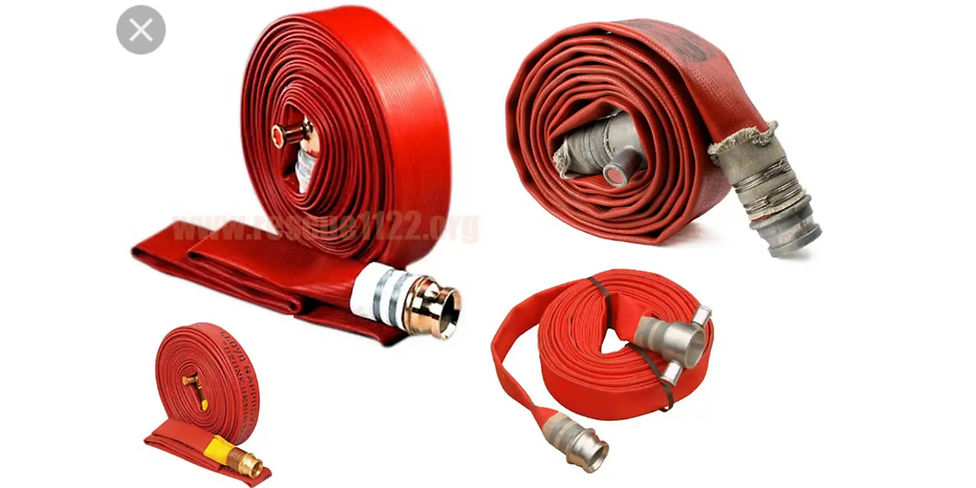
FIRE HOSES
Guaranteed Quality
When it comes to our fire hoses you can count on Kensteve oilfield and allied services Nigeria limited to take care of your every need and guarantee you receive your order in no time at all. We have fire hoses with a high-pressure hose that carries water or other fire retardant (such as foam) to a fire to extinguish it.
it attaches either to a fire engine, fire hydrant, or a portable fire pump. Indoors, it can permanently attach to a building's standpipe or plumbing system
We’re here to see to it that you purchase only the best quality products in the market and will make sure to give you the support and advice you need regarding our goods. Let us know how we can assist you today.

FIRE ALARM SYSTEM
Exceeding Expectations
Our Fire alarm system consists of manual pull stations, visual/audible alarm devices and integrated automatic detection devices; addressable smoke detector/sounder bases and heat detectors located in individual sleeping rooms, corridors, common areas and mechanical spaces.

FIRE NOZZLES
Satisfaction Guaranteed
Our Fire nozzles can provide a constant flow or allow firefighters to select the most appropriate flow rate and operating pressure for fire fighting. A fire nozzle connects to a fire hose to deliver water or fire fighting foam to extinguish a fire.

FIRE MEN GEAR
Committed to Quality
Our Bunker gear (also known as turnout gear, fire kit and incident gear) is the personal protective equipment (PPE) used by firefighters. The term is derived from the fact that the trousers and boots are traditionally kept by the firefighter's bunk at the fire station to be readily available for use.

FIRE ALARM BELL
Exceeding Expectations
A fire alarm bell is an active fire protection component. It uses audible stimuli to alert the occupants of a fire or other emergency condition requiring action. Manual call points are used to initiate an alarm signal, and operate by means of a simple button press.
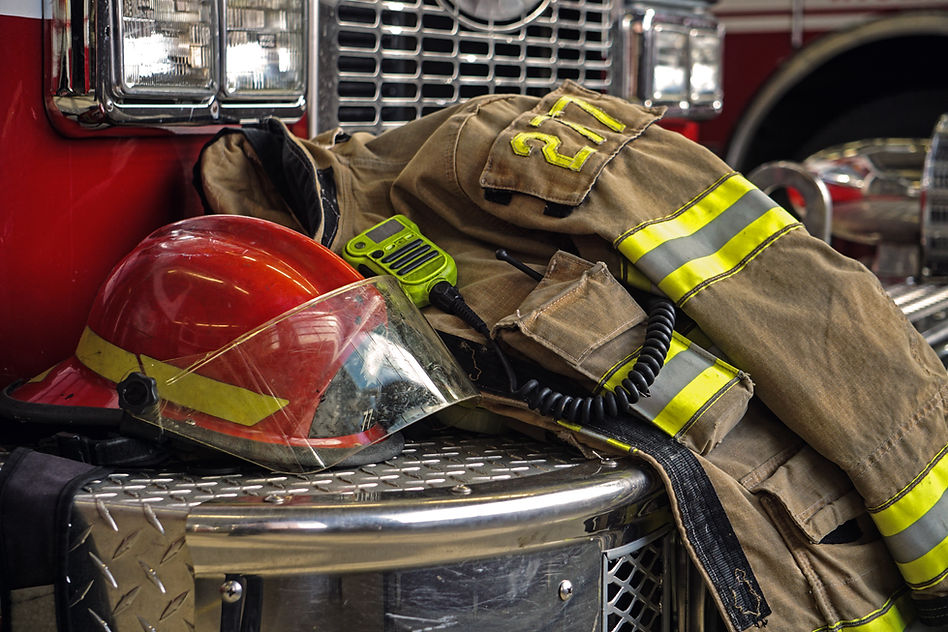
SERVICE
FIREMEN SUITE
FAQS
The Answers You’ve Been Needing
WHICH FIRE EXTINGUISHER SHOULD I USE?
Not all extinguishers are created equal. In fact, there are different fire extinguisher classes designed to put out various types of fires. If flames break out in your home, office, or other building with ordinary combustible products, flammable liquids, and electrical wiring, a multipurpose ABC fire extinguisher is the proper tool to douse the blaze.
For cooking fires in commercial kitchens, a Class K extinguisher is needed to put out the fire and prevent it from reflashing. Class D extinguishers are less common and are only used to fight fires that break out in chemical plants and industrial facilities with combustible metals onsite, such as sodium, potassium, titanium, and magnesium.
For more information on fire extinguishers, contact KENSTEVE OILFIELD AND ALLIED SERVICES NIGERIA LIMITED online or by calling 08166994310.
HOW MANY FIRE EXTINGUISHERS ARE REQUIRED ON A BUSINESS PREMISE?
The ultimate answer to “how many fire extinguishers does my building need” is: It depends.
Factors that determine the fire extinguisher requirements include:
Size and layout of the room: a basic
National Fire Protection Association (NFPA)
rule is that there should be no more than 75 feet between fire extinguishers and that they should be accessible. Naturally, then, the square footage contained in a building and its layout will determine the number needed.
Fire hazard level of the building: public buildings are evaluated and assigned a fire hazard level based on their purpose and what they contain:
Occupational Safety & Health Association (OSHA)
standards, if flammable liquids or gas are stored in quantities of 5 or more gallons, there must be a fire extinguisher of at least a 10B rating kept within 50 feet of the container.
Stairwells: in multistory structures, a minimum of one fire extinguisher must be placed adjacent to the stairway.
For more information on fire extinguishers, contact KENSTEVE OILFIELD AND ALLIED SERVICES NIGERIA LIMITED online or by calling us at 08166994310
HOW OFTEN DO I NEED TO REPLACE MY FIRE EXTINGUISHERS?
Because fire extinguishers come in different sizes, are made of different materials, and contain different extinguishing agents, there isn’t a standard timeframe for replacing them. The best way to make sure your extinguishers are usable is to have them inspected annually. Then, subjecting the cylinders to internal inspections, pressure tests, and recharge services roughly every six years can keep them in service for decades.
However, you should replace your fire extinguishers if you ever notice problems during an inspection, such as a rusty or corroded cylinder, missing or damaged components, inaccurate gauge readings, or missing inspection label. If a cylinder fails a pressure test, this is also an indication that you should discard it and replace it with a new one.
For fire extinguisher replacement services anywere please Contact our experts online or by calling us at 08166994310
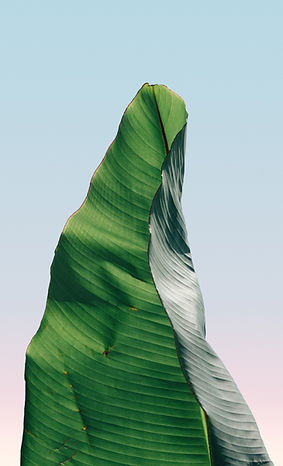
Leave us a message and we'll get back to you.
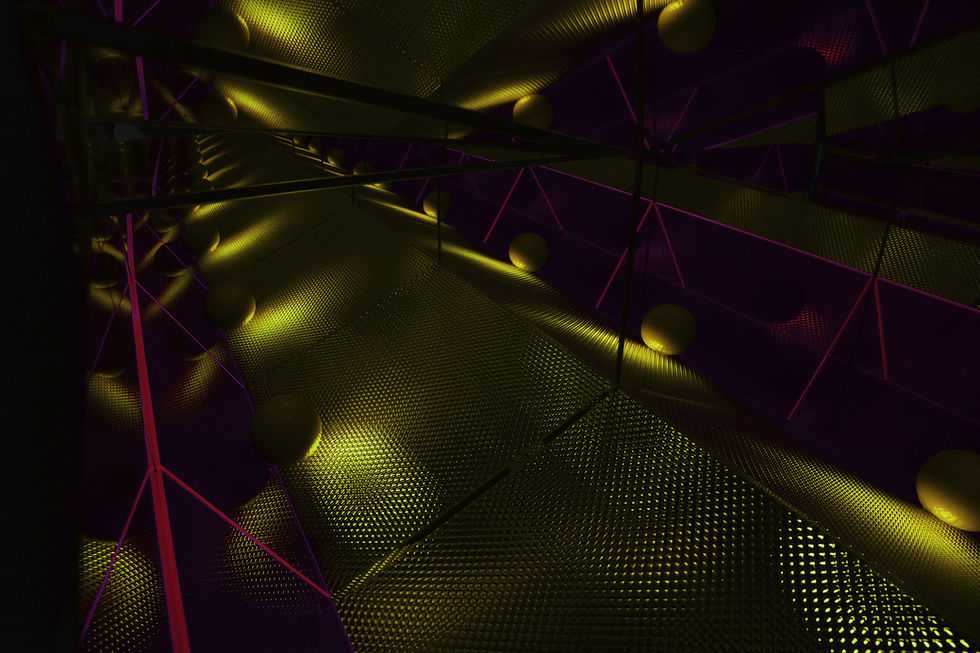
OPENING HOURS
Come Visit
Mon - Fri: 8am - 5pm
Sat: 10am - 2pm
Sun: Closed

